Safety for road and sky
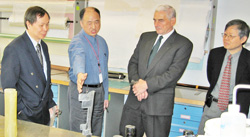
During a recent tour of the labs in the new EV building, President Lajeunesse spent considerable time in Suong Hoa’s composite materials facility. Above, research associate Ming Xe explains the development of an airplane component. Professor Hoa is on the left and Vice-Provost, Research Truong Vo-Van on the right.
Photo by heng wang
When you’re driving down one of Montreal’s highways, hemmed in by giant transport trucks, give a thought to Subhash Rakheja. The engineering professor is doing his best to keep you safe.
It’s a challenge. The transportation sector in Canada is worth about $100 billion a year; it’s highly competitive, and operators don’t spend extra money willingly.
“Freight transportation underwent major change in the mid-1980s, when I was getting started in my research,” he said at a presentation on Jan. 30. He was one of three researchers who gave a summary of their work at a show-and-tell session for the benefit of President Claude Lajeunesse and interested faculty and graduate students.
Rakheja said the regulations have allowed trucks to become significantly heavier and larger. Tank trucks carrying liquids are especially risky, as they can lose control while braking and turning, especially if the tank is only partly filled. Accidents involving such vehicles could be catastrophic.
He works on solutions such as modified triangular tanks that are more stable than the cylindrical ones, and anti-sloshing devices to go inside the tanks. Since the onset of a rollover usually starts at the rear axle of a long tractor-trailer combination, Rakheja is trying to develop a warning system to enable the driver to take corrective action as early as possible.
At CONCAVE, the Concordia Centre for Advanced Vehicle Engineering, researchers test buses and other vehicles for vibration, which can have serious effects, particularly on professional drivers.
As an expert in ergodynamics, Rakheja and his colleagues study the interaction of many factors —the vehicle, the road, the cargo and the driver. They’re trying to develop simulation tools to analyze vehicle-cargo interactions, and create vehicles adapted for our ability to perceive an emergency and react appropriately.
Rakheja also works on the design of tools to minimize their negative impact on our bodies. He showed a sobering photo of the hand of a longtime stone-cutter whose fingers were white and numb after years on the job. He added gently, “In a cold climate, recovery is very slow.”
He has an international reputation and has received many grants over his 20-year career from the major granting agencies and government departments of transportation. A PhD alumnus of Concordia and a 25-year veteran of the engineering faculty, Rakheja was the 2004-05 senior recipient of the Concordia University Research Award.
Rakheja sees his research as an essential part of his mandate as a teacher, because building research models gives his graduate students invaluable practical experience.
At the same show-and-tell, Narayanswamy Sivakumar presented an overview of his work in laser metrology and laser micromachining. Nadia Bhuiyan was prevented by illness from presenting, but master’s student Adil Salam presented an overview of her work in industrial engineering. Bhuiyan uses “lean engineering” to guide the development of a new product from concept to launch.
Many composites projects
President Lajeunesse must have been impressed by the number of major projects in Suong Hoa’s composites lab when he toured it in January.
The lab is involved in a $2-million project on the use of composite materials for the manufacturing of aircraft components. Specifically, it is developing a wing box using bonding technology.
Its collaborators are many: researchers at the École Polytechnique, two institutes of the National Research Council
Canada and the Defense Research Establishment Val Cartier, plus Bell Helicopter, Pratt & Whitney and Delastek (a small company in Quebec). The work is supported by the Consortium on Aerospace in Quebec (CRIAQ).
Hoa’s team is also working on the use of thermoplastic composite for the manufacturing of helicopter landing gear and wing box panels for Bombardier aircrafts.
This again is supported by Bell Helicopter, Bombardier, and CRIAQ. It is a collaborative effort with ETS and two institutes of the National Research Council of Canada. The cost of that project is about $450,000.
The composites lab is involved in a project on self-healing materials with the Canadian Space Agency and MPB Technologies, and several projects on nano-technology.
“We have developed nanocomposites that are fire self-extinguishing and impact-resistant,” Hoa said.
Three companies have signed up to exploit this technology through a patent applied by Gestion Valeo on Concordia’s behalf.
The next research presentation will be on the theme of Learning, Human Development and Human Environment and will take place on Feb. 27 from 3:30 - 5 p.m., location to be announced.
The presenters will be psychologist Mark Ellenbogen, biologist Vincent Martin and education researcher Philip Abrami.